Products
01
Grindex
Production program
What we produce
We manufacture wide range of cylindrical grinding machines – different sizes, standard and grinders produced based on individual customer requirements, universal machines for flexible and mass production. They can be in the basic version, cells with different combinations of grinding – in single or multi set up, manual or automatic loading.
The complete production process is performed in-house, starting from cast parts production, heavy-duty and precise machining, mechanical and electrical assembly, hardware and software installation, laboratory tests, component prove out, painting. Purchased parts are from renowned world manufacturers.
Grinders comply with CE regulations. Geometrical and operational accuracy is checked and documented by appropriate test protocols based on ISO, VDI/DGQ, GOST standards, as well as on the basis of specific customer requirements for the accuracy of ground work parts.
Since in Europe we belong to the so-called “area of low costs”, we are able to offer a more favorable price for the same quality compared to the competition.
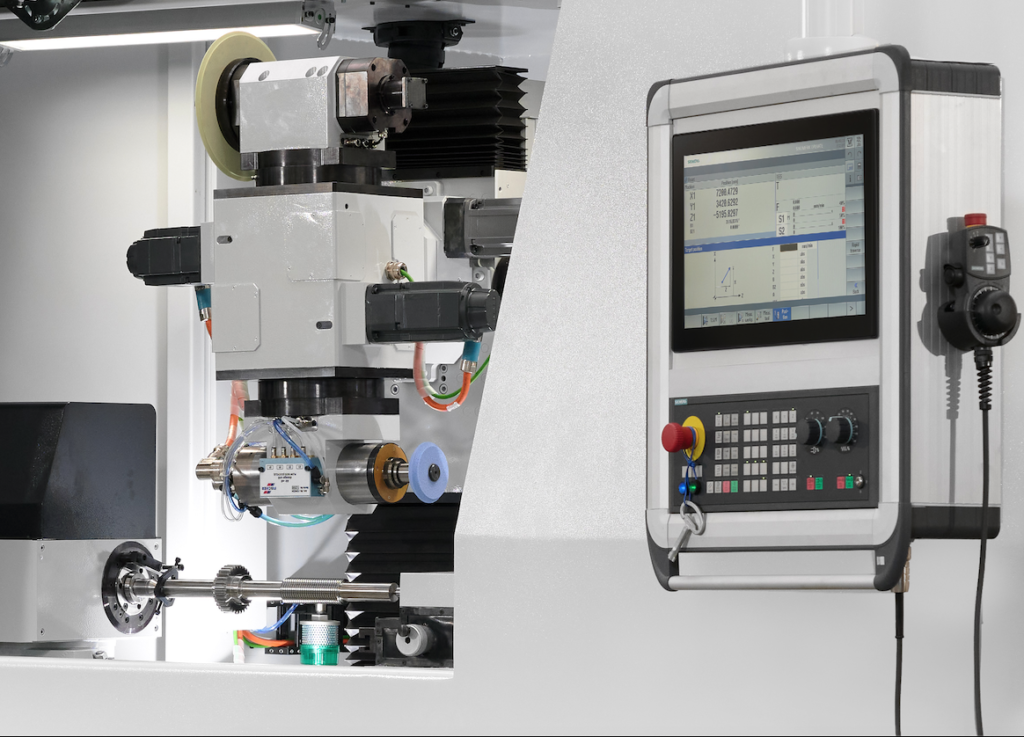
Basic types and models
All basic types are functionally universal machines with the possibility of combining external, and internal grinding, face, taper, metric thread. Models “BS – B, C, D, E“ are of similar design and the main difference between them is in the size of the assemblies, i.e. the dimensions of the work parts that can be ground, which is up to 4000 mm in length, the largest swing over diameter 1300 mm and the weight up to 2500 Kg.
The guideways, one straight and one “V”, are manually scraped and covered with anti-friction material, which ensures continuous movement, high accuracy and repeatability.
The wheelhead can be left and right make, or fixed for certain angle. For wheel diameters higher than Ø250 mm, the dynamic wheel balancing system is available.
The tailstock is with hydraulic opening, manually adjustable clamping force and taper error correction feature.
Internal grinding spindles may be belt driven of high-frequency (HF), with direct drive and water cooling system, permanently greased or lubricated with oil mist.
Automatic grinding cycle with oscillating, plunge-cut or interpolation method. Rapid travel, rough and fine grinding, spark out, automatic compensation of grinding wheel wear. Possibility of set up and operation in manual mode.
Basic types and models
Models “UB – C, D, E” – internal grinding of cylindrical and taper holes, internal and external face. These are derived from basic models of external grinding machines, by placing internal grinding spindle on the wheelhead. It is mainly suitable for deep hole grinding, but smaller sized parts can also be ground.
Maximum internal grinding diameter is Ø600 mm and grinding length up to 1200 mm, depending on the selected model. Limitations in work part size are related to hole diameter and length ratio.
“MBU” model is suitable for grinding large diameters – up to 1000 mm. The design of the machine bed and the machine itself is based on American manufacturer “Bryant”. The MBU model range also includes the MBU 80 type, which is designed under the German license “Fortuna Werke” and is intended for grinding holes of smaller dimensions – Ø3 – Ø80 mm. This machine is completely different in design from other MBU models in the production program.
Model “BBN” is suitable for cutting from solid material and external thread grinding – all types of threads, worm shafts, slots. The smallest external grinding diameter is Ø1 mm and Ø300 mm is the largest one. Maximum thread length is 1200 mm on model BBN 1600. Minimum thread pitch is 0,2 mm.
Model “BBUN” is the machine for internal thread grinding, with internal thread range Ø3 – Ø200 mm. Maximum thread length is 120 mm. Minimum thread pitch is 0,2 mm.
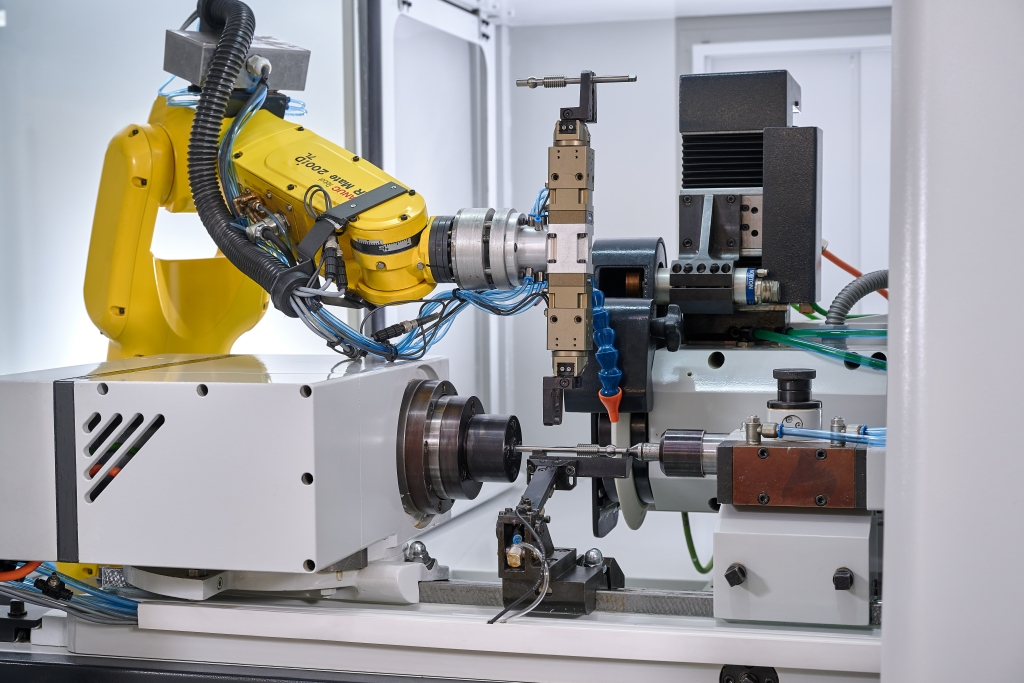